Behind the Seams: A Conversation with Hardesty Dwyer
We had the pleasure of sitting down with Amanda Hardesty Dwyer to learn about her path to running a successful custom upholstery workroom in San Francisco. The Niche Interiors designers have collaborated with Amanda and her talented team for years to design high-end, bespoke upholstery for our San Francisco Bay Area interior design clients. Custom upholstery is a key component for our interior design studio – it allows us to create unique furniture pieces that are tailored perfectly for a home. Amanda’s attention to detail, focus on sustainability and passion for the craft of fabricating high-quality upholstery make Hardesty Dwyer a natural partner for us.
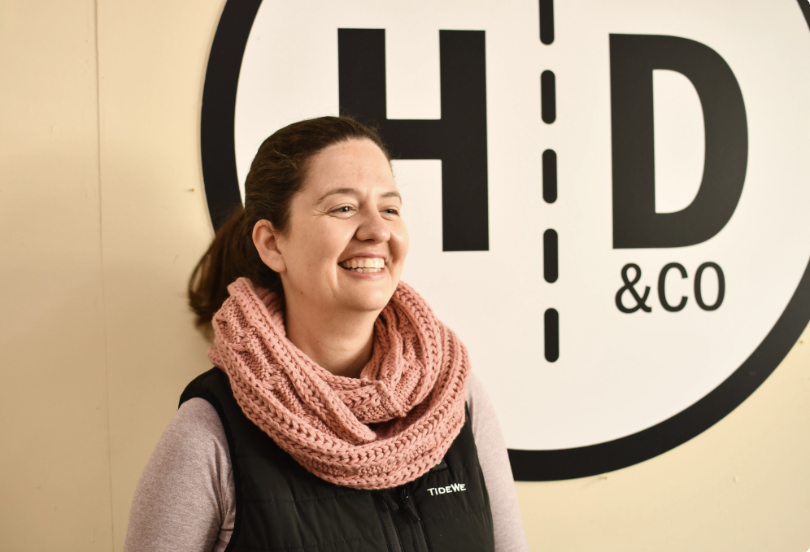
NI: Tell us about your background and what led you to owning a custom San Francisco upholstery workroom?
HD: First, thank you! We appreciate the kind words – it’s always amazing to hear that clients are appreciating the incredible energies my team puts into every custom piece of furniture. In retrospect, my career started in my parent’s basement on hot summer days. I grew up in a very rural community in a home without air conditioning and we often retreated to my mother’s sewing room when it got hot. I learned to sew and create from a very young age mostly to stave off boredom and heat. I was also lucky to have a carpenter father and grandfather. Dreaming up designs and executing them was another great way to fill time with my brothers. It was FUN! We got to use tools and make something from nothing. Of course I had no idea these would be such integral skills in my future.
A few years after college I rolled into San Francisco with my boyfriend and a journalism degree and got extraordinarily lucky to land an admin job with Richard Andronaco Upholstery in 2008. I rapidly started working on the production end, while running the office, and over the next 9 years Richard gave me all of the skills I needed to understand and execute a custom upholstery studio in the highest end market. As Richard was approaching retirement he asked if I wanted to take over and carry on the business. That’s just what I did in January of 2017! A small shop (5 employees) at the time, we transitioned the company to Hardesty Dwyer & Co and have been blooming ever since.
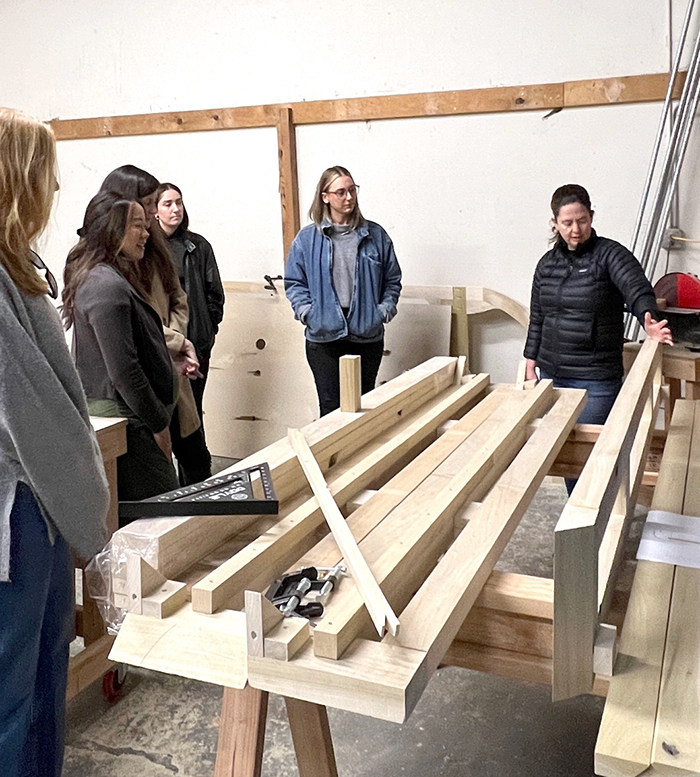
NI: What gets you excited to come to the workroom every day?
HD: People and problem solving. I’m extremely lucky and have worked hard to build an environment where people want to work, including myself. I’ve not always been successful, but I’ve always tried. The team of craftspersons and supporting staff at HD&Co are amazing. I’m lucky to spend my time with them every day. The great attitudes brought by my team make the stressful task of daily problem solving a lot more collaborative and fun. As a custom workroom, we rarely make the same piece of furniture twice. Every day we are creating something from nothing and making sure that it’s exactly what our client had in mind. We literally bring dreams to life, a challenging and extremely rewarding way to spend the day!
NI: Can you explain the process for building a new piece of furniture from start to finish?
HD: Absolutely! In short: Get design. Make drawing. Build frame. Make groundwork. Get approval. Upholster. Make Cushions. Check Work. Send home. 🙂 When we are starting on a new piece it begins with a review of the information provided to us by the interior design firm and a conversation about details that we need to nail down prior to the build. This can include mattress dimensions if we are building a custom bed or seat depth if we are building a custom sofa. If the interior designer’s client is unsure, this is an opportunity to meet face to face and do a mock up sit test! We do these in the studio and it’s a way for us to determine the homeowner’s desired comfort level, how they sit in the piece and all of the dimensions we need to make the piece perfectly comfortable for them. We are making bespoke items, so this step is like getting measured for a custom suit.
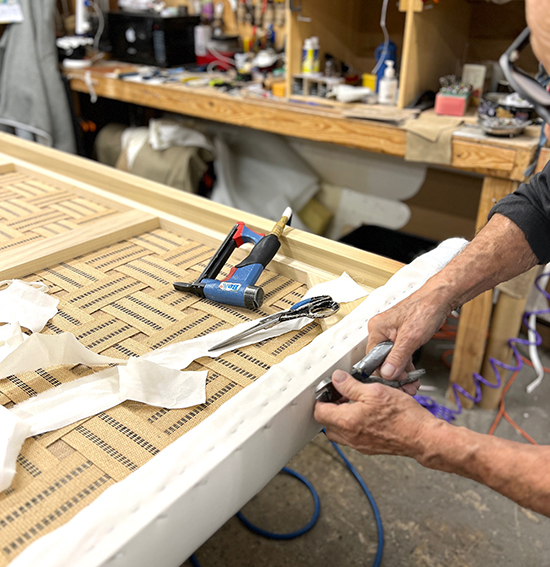
With these details in hand, we start the process of designing the internal frames. I think this step is the most critical because we are building the skeleton and it not only needs to be extremely strong, but also dimensioned correctly so when we start to add padding and shaping it gives us everything we need to hit the final dimensional marks. We do full fabrication drawings in Sketch-up and these drawings go out to our interior design clients for red lines. Then we are given the green light and can ACTUALLY start building a piece of furniture! The CADs then go to our frame builder. At this stage we have someone on the team who was NOT involved in the build double check all of the dimensions on the frame and make sure it matches our order.
Now, on to the groundwork! The first stages of the upholstery process, everything before the final fabric goes on, is called groundwork. We start with creating a latticework of tensioned jute webbing on the bottom of the piece, which creates a place to attach and support our coil springs. Individual coil springs are then placed and attached, then hand tied together with jute twine into a single unit. The next few steps involve adding springs to the back, using burlap and cotton and needles and thread to complete the initial base layer of groundwork. Next, we move onto the foaming of the piece. This is where the bare frame takes shape into its final form. This stage can involve poly or latex foam, dacron or wool, edge rolls and muslin and staples and tacks. At the end of this stage, our piece will look be in its final form, but upholstered in a muslin textile. At this point, our clients are invited back into the studio to review the piece, make any adjustments, and approve before we begin cutting the final textile!
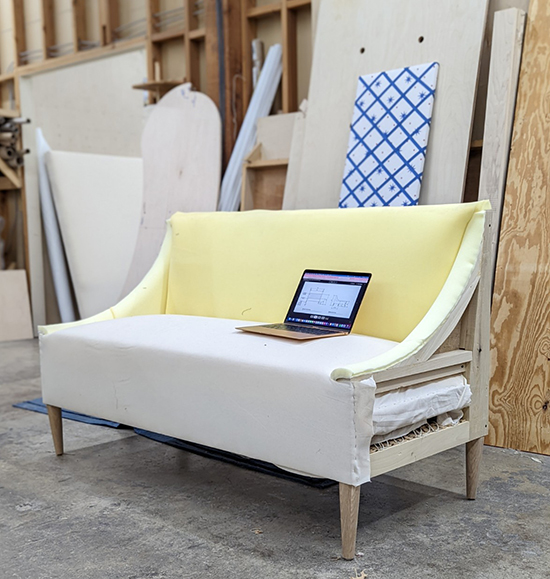
Next is the fun part! Fabric is cut and sewn by our textile team and passed to the upholsterers. The final fabric is applied over the muslin and the piece finally comes to life!! During this process, any exposed wood items would have traveled to the finishers and returned back to our San Francisco studio in time to be attached after the final fabric. Then it’s back over to the textile team for cushions. We cut and fill all of our inserts and down pads in house, so this is usually another week long process as templates are made, down pads are cut and sewn, foam inserts are created and the final fabric covers are also made. Once the cushions are on the piece we can ALMOST call it done! The project passes back to our front end team where it is reviewed and signed off on by 2 different people to make sure we got it right. Our beautiful new creation is photographed, covered and is finally ready to head off to its home!
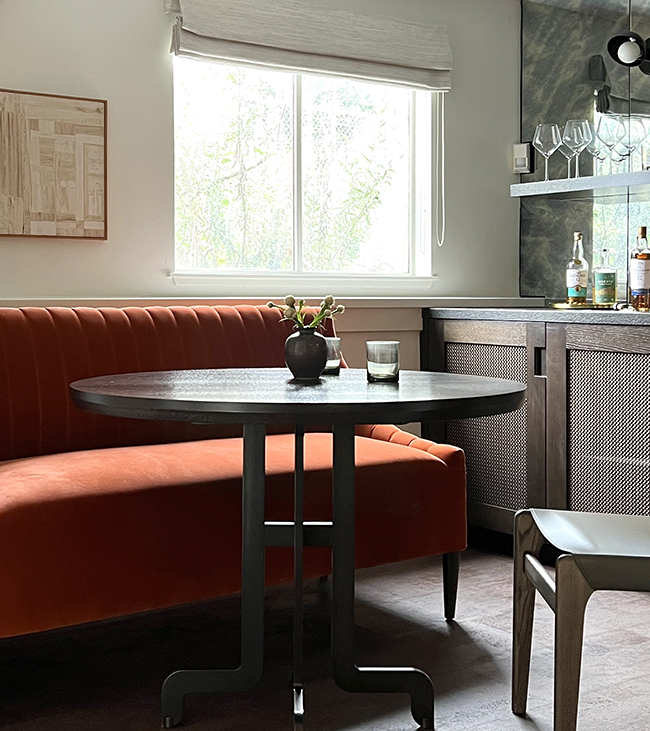
NI: We know you are as passionate about sustainability as we are. How important is it in your work and what practices have you integrated into your business that set you apart from other Bay Area custom upholstery workrooms?
HD: Yes! Many of our build and business practices have been put in place because not ONLY are they the best choices for my employees and the product, but for the environment too! Our choice of materials is key. Poplar is a fast grown, off cut tree from the West coast and the only wood we use to make our upholstery frames. We use natural textiles as often as possible including muslin fabric, jute webbing and twine and burlap. Some clients prefer the use of Poly foams, so we have chosen to use the highest quality poly on the market so it gets a maximum use life before needing to be replaced and go into a landfill. We are able to build 100% green upholstery as we’ve worked hard to create fabrication styles that include latex foam and wool to swap out the very few non-compostable elements in our standard builds.
We have also partnered with various organizations in the city so our foam, dacron and fabric scraps all have a second life! We also sort and recycle aggressively. Our studio produces one standard black bin of actual trash per week. That might still seem like a lot, but for a manufacturer it’s something we are really proud of!
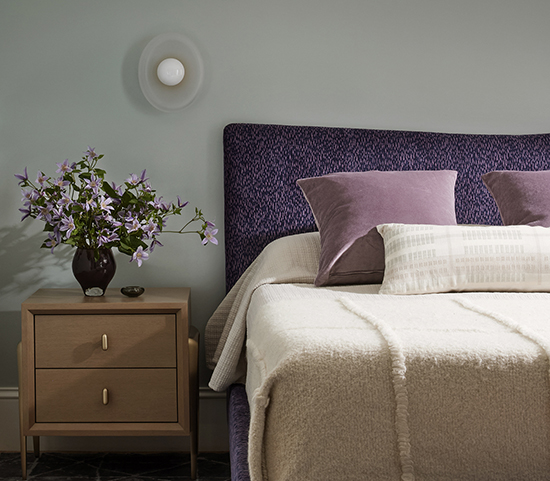
NI: We love collaborating with your team to design and create furniture that’s unique to each of our clients. What advice would you give interior designers when they are starting to design a custom piece of upholstery?
HD: My best advice is to find a fabricator you communicate well with! Our best collaborations are the ones where we all come to the table with respectful ideas and share our strengths with each other. I think of myself as the engineer, analyzing designs to make sure we not only hit the aesthetic goal laid out by the interior designer, but the comfort goal as well. When you start designing, it’s totally OK to not know the best seat depth or pitch, that is where your trusted upholstery partner’s expertise comes into play!
Head to our custom furniture page to get inspired by what we have designed for our San Francisco Bay Area interior design clients!